The main objective of the SEABAT project is to develop full-electric Hybrid Energy Storage Systems (HESS) for large marine applications. The so called HESS would be a modular combination of high energy and high power batteries. The modular approach for such a system is important, since modularity can reduce the individual component costs of the battery system (cells, converters, etc.) by introducing profits from large scale manufacturing of standardized low cost components for every unique ship design.
When designing a full-electric ship, the usual approach is to have a single type of battery on-board as the main power source. Depending on the operational conditions of the ship, shipbuilders usually decide upon a single type of battery system. The decided battery system is usually oversized in order to accommodate for a large number of different operating conditions and also to guarantee the required lifetime. For example, a full-electric Harbor Tug would require very high power output from its batteries during its working condition, whereas, while normal cruising operation the power demand is very low. If the battery system is built with only High Power type batteries, the shipbuilder will end up oversizing the battery system to accommodate for both operating conditions. Thus, a combination of High Power and High Energy batteries would result in a more optimized Battery System size leading to cost reduction. Figure 1 below shows a representation of how using only one type of battery may lead to oversizing of the battery system. Apart from the power and energy rating of the batteries, the number of charge/discharge cycles also needs to be considered. Thus, two different approaches were considered to determine the effectiveness of such a HESS for various applications. The first approach is called the Cycle analysis, where the energy, power and number of cycles required by individual vessel type are used to determine the specific type of battery required. The second approach is based on the theory of C-rate optimization, where two different types of batteries are combined in a HESS to match the C-rate requirements of an application.
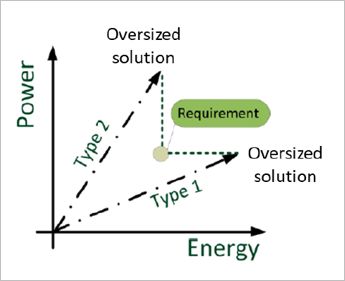
Since operational profile of vessels very rarely consist of a single type of cycle for the batteries, for 34 vessels investigated, the operational profile was separated into a primary cycle and a secondary cycle. The primary cycle is defined as the most common type of operation and therefore results in a higher number of cycle and usually a smaller energy requirement. The secondary cycle is defined as the alternative operation, which is performed less often by a vessel, but usually has a strong impact on the energy requirements of the battery system and therefore on the size and design of the battery system. Both the primary and secondary cycles have been analyzed for 34 different types of vessels and were grouped into application types based on their C-rate and cycling requirements according to the definition in Table 1, which are identified as the basic requirements for battery system initial design.
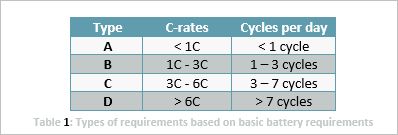
There is a large difference in operational requirements for marine battery systems, which makes it impossible for a single type of battery technology to be optimal for all applications. This rules in favor of investigating the HESS concept. Where most marine battery systems currently on the market are designed for the average requirements of vessels, the combination of a high energy battery systems with a short cycle life and a high power battery system with a long cycle life can potentially improve the efficiency of battery usage in the marine market.
To understand the performance of such a HESS for large marine systems, it is also important to know the performance of current battery technologies available for the marine systems. Thus, a performance analysis of 30 different battery systems from 15 suppliers was performed. The analysis of these 30 battery systems was performed by considering the following 9 main parameters: Costs, Energy, Power, Lifetime, Thermal Management, Safety, Mechanical Integration, Electrical Integration and Battery Management System. These 9 main parameters are further divided into 33 battery system properties for all 30 different battery systems. In order to compare the performance of all 30 battery systems, a score based comparative study was performed by giving every battery system was a score ranging from 1 to 5, where 1 being the lowest score and 5 being the highest score.
After considering the three basic requirements for battery selection (energy, power and number of cycles) led to three different types of batteries: High Energy Batteries, High Power Batteries and Heavy Duty Batteries. Taking a closer look into the analysis between the maximum continuous discharge C-rate and the gravimetric energy density another group of battery systems is discovered, the Medium Energy batteries. This can be seen in Figure 2.
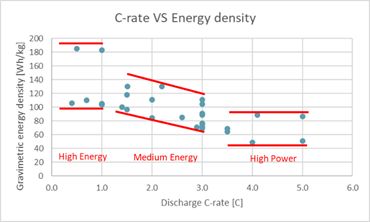
The heavy duty batteries distinguish themselves by the number of cycles they can perform at a Depth of Discharge (DoD) of 80%. Figure 3 below shows that there is a clear relation between the number of cycles that a battery can perform and the normalized costs per cycled kWh, although the system costs can vary significantly. The group of heavy duty batteries is therefore determined by the normalized costs per cycled kWh below 0.07 €/kWh. Currently the systems with the lowest normalized costs per cycled kWh are at approximately 0.04 €/kWh.
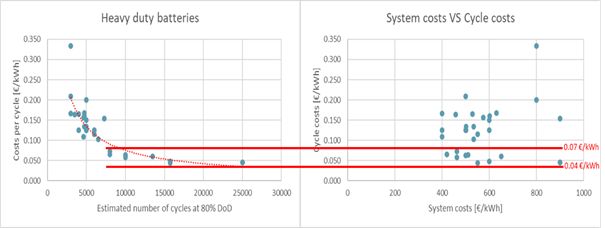
The requirements for heavy duty batteries are based on different specifications compared to the High energy, Medium energy and High power batteries and therefore it can be that a specific battery system can be classified as a heavy duty battery as well as one of the other types. Therefore in total there are six different basic types of battery systems defined, as shown in the Figure 4.
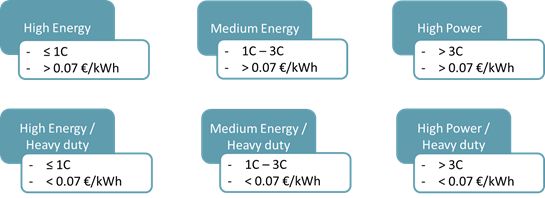
After analyzing all 30 different battery systems from 15 manufacturers, it was concluded that the battery systems were available in four different designs: Modules, Trays, Racks and Blocks. Each battery system design type has its own advantages when used for specific types of vessels. Thus, it becomes very important to consider the type of system design of a battery system before integrating it on the vessel. Performing the score based analysis, by considering all 33 parameters of the 30 different battery systems, the overall average score of the battery systems categorized by their system design can be seen in the table below, where 1 is the lowest score and 5 is the highest score.
